As with compression molding, transfer molding requires secondary raw material preparation into pre-forms. It differs, however, in the placement of these pre-forms into a “pot” located between the top plate and a plunger. When the pre-forms are placed into the pot, the mold is then closed and the material is compressed by the plunger and transferred through sprues into the cavity below.
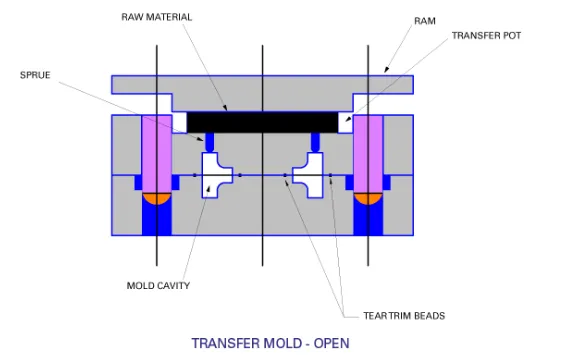
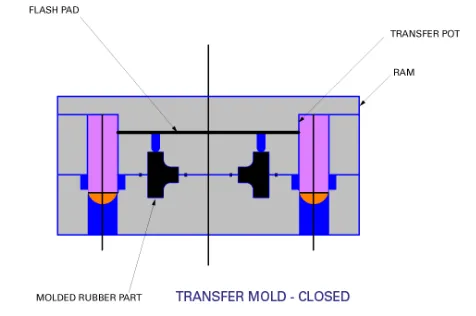
Some possible advantages of transfer molding over compression molding can include:
- High Cavity Count – In many cases, transfer molded rubber products require fewer and simpler pre-forms. One pre-form can fill hundreds of cavities
- Cost effective tooling
- Tighter control of dimensional tolerance – the mold is not held open by excess material spilling out of the cavity parting line; all the excess hold the plunger open from the pot
- Economical process for medium to high precision components
- Color molded rubber parts benefit – pre-forms can be cut by hand from raw material, thus reducing the chance of contamination that can result from the mechanical prep of compression molding or the injection screw and barrel in injection molding.
- Capable of producing overmolded components
The primary disadvantage of transfer molding is found in the increase of waste or excess flash. This can be seen in the “flash pad” or the rubber left in the pot after the transfer is cured which can either be recycled or discarded.
Comments are closed.